
Cooked Bioplastic
Air filters and Anti-bacterial Textiles
I started out to create two different bioplastic materials, one filtered by plants and the other by activated carbon with the goal of comparing the effectiveness and the efficiency of both. One feature that's required for both materials is high resistance to water. After some research on the principles of spherification using sodium alginate and calcium chloride, I decided to apply this principle to create water resistant bioplastic mediums.
An Overview of The Process of Spherification
Spherification is a culinary process that employs sodium alginate and either calcium chloride or calcium glucate lactate to shape a liquid into squishy spheres.
Equation 1: Sodium alginate (NaC6H7O6) can react with calcium chloride (CaCl2) to make calcium alginate (C12H14CaO12).
2NaC6H7O6 + CaCl2 = 2NaCl + C12H14CaO12
This reaction results in the creation of an hydrophobic semi-solid impermeable membrane.
Applying this principle to our research meant our mediums must contain sodium alginate and be exposed to calcium chloride salt in order to be water resistant.
The materials used generally in the course of this research are: Sodium alginate, calcium chloride, agar agar, gelatin, glycerin, activated carbon, olive oil, vinegar and water.
Plant Filtered Bioplastic
Some small plant tissues have the ability to grow into full grown plants in a growth medium - an ability called Toti-potency. This served as the inspiration to create the plant filtered bioplastic.
To successfully grow plants in a solid water resistant bioplastic medium, it was necessary to create a medium that could support plant life in terms of strength/flexibility, resistance to infections. 7 different recipes were experimented with and the results of those experiments are included in this report. These 7 recipes can be classified in three categories, Pure sodium alginate recipe, Sodium alginate with agar agar recipe and Sodium alginate with gelatin recipe. A mix of calcium chloride with water at a ratio 7:100 was used for all the recipes and experiments.
1. Pure Sodium Alginate recipe
First alginate and glycerine were mixed together and then added to water on heat. The resulting solution was then poured over a silk screen frame after which the calcium chloride solution was sprayed on using a spray bottle. This was left for 5-10 minutes before being rinsed with cold water and left to dry on the frame. It took about 7-10 days to dry.
The bioplastics created from this recipe were too stiff, inflexible hence could not support plant life.
2. Sodium alginate + Agar agar recipe
Agar and alginate were mixed together with water and left on heat till the solution started bubbling.
Varying amount of agar, alginate and glycerine were added in different trials and the resulting solutions were then cast into silk screen frames, afterwards treated with calcium chloride like in the first trial.
The bioplastics produced from these were also stiff and inflexible.
3. Sodium alginate + Gelatine recipe
After various trials, I found that it was best to split the glycerol into two parts, one part was added directly to the gelatine with water solution and the other mixed in a separate bowl with sodium alginate. The sodium alginate mix was then added gradually in small bits to hot water. This yielded better transparent homogenous solutions and the resulting bioplastics were not infected.
The bioplastics created from the first trials were quite flexible but were covered in mold after 4-7 days.
After Adjusting the cooking method, transparent bioplastics that had thin textures which also showed more resistance to molds were obtained.
Some plant life were introduced into the solution after cooling, watered twice daily and dehydration rate of these plants were studied.
Currently, plant growth hormones like auxin are being added to the recipe and the growth behaviour of the plant materials are being monitored.

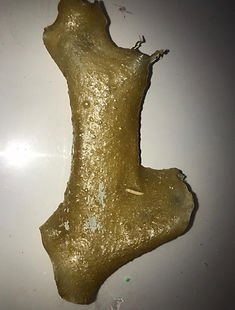




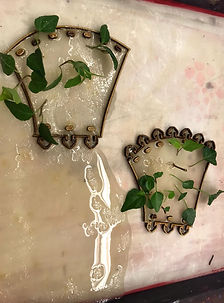


Activated Carbon Filtered Bioplastic

To successfully create a carbon bioplastic that was capable of filtering air, there has to be a particular amount of activated carbon and that was one of the goals of this aspect of the research work, the second being to create a flexible material that felt comfortable on the human skin.
2 different recipes with varying quantities of ingredients were experimented with and the results of those experiments are included in this report. These 2 recipes are Carbon, sodium alginate, gelatine recipe and Carbon with gelatine recipe. The carbon with gelatine recipe was adopted in response to the fact that most of the experiments with alginate included yielded mold infested bioplastics.
1. Carbon + Gelatine recipe
Gelatine was mixed with water, left to thicken and heated till it became liquid. Glycerine and carbon were added after while on the stove. This mixture was then poured into a frame and left to dry. It took between 3-7 days to be completely dried and ready to use. The bioplastics obtained from the resulting solutions ranged from highly flexible and strong to rigid and fragile.
2. Carbon + Sodium Alginate + Gelatin
The method of cooking applied here is the same as that used in the sodium alginate + gelatine recipe listed above under the plant filtered bioplastic, the only difference being the activated carbon which is added to the mixture while on heat.
The first few trials produced bioplastics that had the desired level of texture but were covered in mold after 4 days.
I adjusted the recipe, adding more water, activated carbon, glycerine and creating the right balance between Sodium alginate and Gelatine. The resulting bioplastics from the new recipe were flexible, soft-textured, water resistant and remained clean and free of infections even after 2 weeks.
Using the laser cutter, raster engravings were made on the final samples, laser cut and assembled using interlocking joints to make a mask.
The antibacterial properties and degradation rates of the final water-resistant carbon bioplastic samples on land, air and water are now being tested.
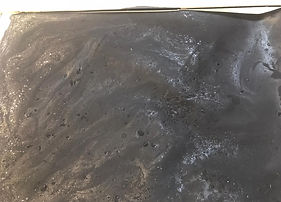

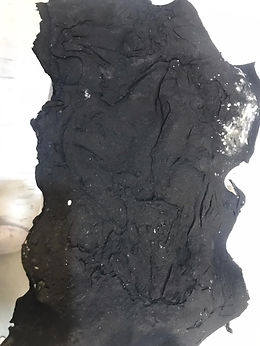

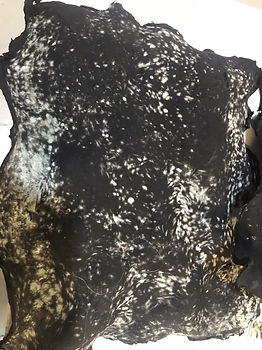


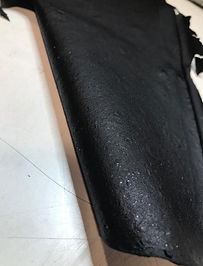
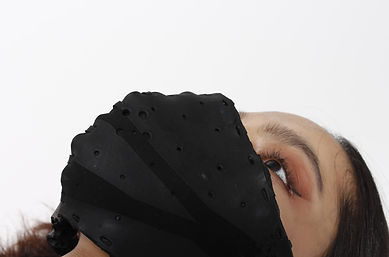

